Aufbau & Prüfung HochspannungsKabel
Kupfer oder Aluminium
Leiter Hochspannungskabel
Der Kabelaufbau ist immer ähnlich. Zunächst wird für die Stromführung ein Leiter benötigt. Dieser kann aus Aluminium oder Kupfer sein. Kupfer ist der bessere elektrische Leiter und hat bessere mechanische Eigenschaften, aber Aluminium ist leichter und günstiger. Wenn möglich wird der Leiter in modernen Kabelsystemen ein bis zwei Querschnitte höher gewählt und dann bei gleicher Übertragungsleistung Aluminium verwendet. Am ökonomischsten sind hier massive Aluminiumleiter. Sie sind von Natur aus wasserdicht, was bei mehrdrähtigen Leitern nur durch Quellbänder erreicht wird, und ihr Durchmesser ist bei gleichem Querschnitt kleiner. Das hat zu Folge, dass der nachfolgende Kabelaufbau im Volumen auch geringer ist und damit ein sehr günstiges Kabelsystem entsteht. Nur bei hoher Stromübertragung, die auch einen großen Querschnitt benötigen, wird noch Kupfer benutzt oder wenn provisorische Kabel wie Baueinsatzkabel mehrmals verlegt werden.
Segmentierte Leiter
Die Übertragungsleistung kann noch einmal gesteigert werden, in dem die Stromdichte in einem Leiter besser verteilt wird. In großen Leiterquerschnitten ist die Stromdichte außen höher als im Kern. Um das zu verringern wird der Leiter in Segmenten unterteilt, auch Millikenleiter genannt, und in einem Segment wird dadurch eine einzelner Draht immer wieder von innen nach außen geführt. Durch die Kontaktwiderstände zwischen den Segmenten wird die Stromdichte besser verteilt und damit die Übertragungsleistung von großen Kupferleitern, um bis zu 20% erhöht. Mittlerweile werden auch größere Aluminiumleiter ab circa 1600mm2 segmentiert. Der Effekt ist hier nicht so hoch wie bei Kupferleiter, aber es könnte der leichte Gewinn in der Übertragungsleistung dazu führen, einen kleineren Querschnitt auswählen zu können. Bei größeren Querschnitten mit größeren Einzeldrahtdurchmesser oder bei segmentierten Leitern ist es üblich mehrere Lagen leitfähiger Quellbänder und oder Nylonbänder auf den Leiter zu wickeln.
Enamelled oder oxidierte Leiter
Um die Übertragungsleistung weiter zu erhöhen, können einzelne Drähte lackiert oder oxidiert werden. Man spricht dann von enemalled oder oxidierten Leitern und erreicht eine noch bessere Stromdichte im Leiter und damit eine noch höhere Übertragungsleistung. Dieser Leiter wird gerne für Zwischenverkabelungen von Hochspannungsfreileitungen, Anbindung von Kraftwerken und in Großstädten für Wechselspannungs-Höchstspannungskabelanlagen genutzt.
Große Querschnitte für Gleichstrom
Für Gleichstrom Kabelsysteme kann technisch auf die etwas teureren segmentierten oder lackierten Leiter verzichtet werden. Es gibt hier kein Skineffekt wie bei Wechselstrom und damit eine gleichmäßige Stromverteilung. Hier werden dann Rundmehrdrahtige oder geformte Leiter eingesetzt. Es gibt aber einige Hersteller die mechanische Schwierigkeiten mit großen Kupferquerschnitten von 2500 – 3500mm² in der Produktion haben und daher die Leiter trotzdem segmentieren.
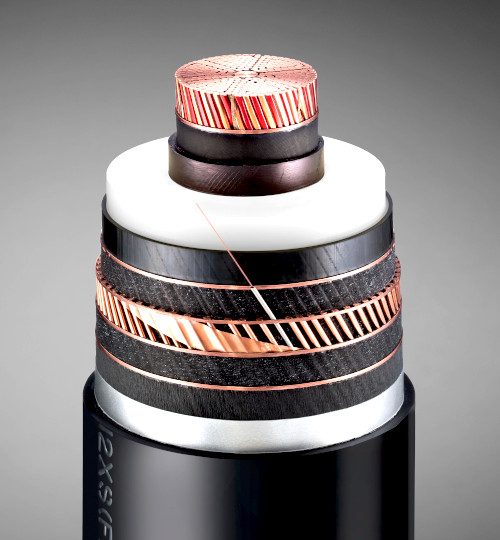
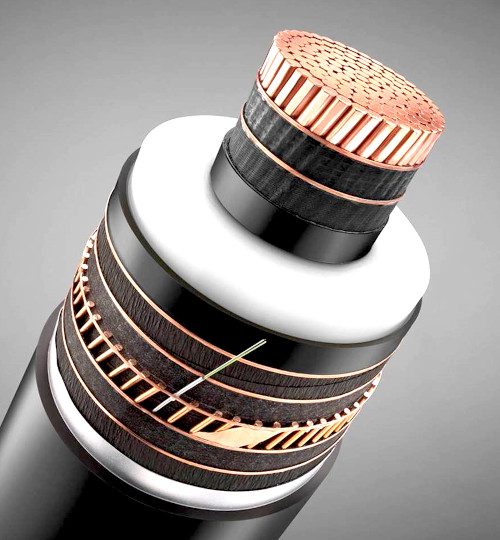
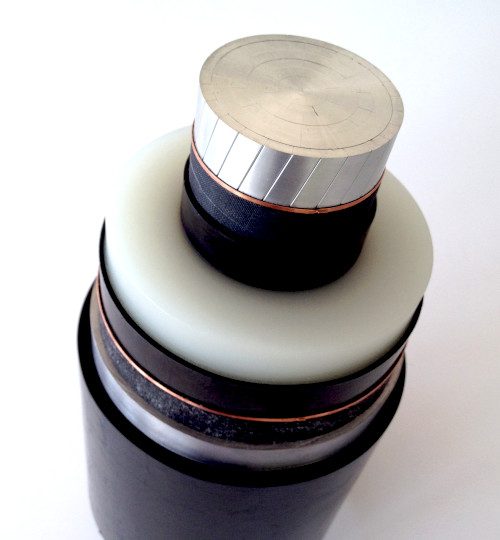
Vernetztes PE
Isolationssystem Hochspannungskabel
Heute wird vernetztes Polyethylen als Isolation bei Wechselstromkabel genutzt. Die Vernetzung von Polyethylen-Ketten wird durch Peroxid erreicht, welches in den Pellets der Hersteller wie DOW oder Borealis meistens schon beigemischt ist. Diese Pellets werden in LKW Containern geliefert und mit Vakuumpumpen in einem geschlossenen System den Extrudern zugeführt. In den Extrudern wird entlang der Extruderschnecke das Hochspannungsmaterial auf circa 120°C erhitzt und vermengt, so dass der Vernetzungsprozess noch nicht startet, aber eine gut vermengte breiige Masse dem Spritzkopf zugeführt wird. Heutzutage werden dreifach Spritzköpfe genutzt, die dem einlaufenden Leiter zunächst die innere Leitschicht, dann die Isolierung und dann die äußere Leitschicht kurz nacheinander „umspritzen“. Die innere und äußere Leitschicht besteht ebenfalls aus VPE, ist aber mit Kohlenstoff (Ruß) gefüllt, um das VPE Material leitfähig zu machen. Die innere und äußere Leitschicht haben die Aufgabe das Hochspannungs- und Erdpotential an die Isolierung zu bringen und den Übergang zur Isolierung möglichst glatt zu gestalten. Dadurch entsteht ein homogenes elektrisches Feld in der Isolierung. Ist die Isolierung durch Verunreinigungen oder Lufteinschlüsse gestört, oder sind die Übergänge zu den leitfähigen Schichten nicht glatt, kann es zu Teilentladungen und dann sehr schnell zu Durchschlägen kommen.
Vulkanisierung im Vernetzungsrohr
Beim Vulkanisieren im Vernetzungsrohr, in dem der Leiter mit dem Isoliersystem wie eine Kette hängt oder in einem Turm senkrecht nach unten, wird durch eine hohe Temperatur über 300°C und einem hohen Druck mit Stickstoff, das auch als Schutzatmosphäre dient, die Vernetzung der PE-Moleküle erreicht. Aus dem thermoplastischen Polyethylen wird ein vernetztes thermoelastisches PE und der Leiter kann mit Betriebstemperaturen bis zu 90°C betrieben werden. Nach der Produktion wird ein sogenannter Hotset-Test durchgeführt, um den Vernetzungsgrad zu kontrollieren. Nach der Vernetzung läuft die Ader, damit ist der Leiter und das komplette Isolationssystem gemeint, in ein Kühlrohr ein, um die Ader abzukühlen und auf eine Kabeltrommel aufrollen zu können. Anschließend wird die Ader in einer Temperkammer in Abhängigkeit ihrer Isolationsdicken 1-2 Wochen entgast. Während des Extrusionsvorganges sind Beiprodukte wie Methan entstanden, die reduziert werden müssen, bevor die Kabel metallisch ummantelt werden. Schwierig ist es bei der Produktion die „Rundheit“ der Ader einzuhalten, besonders wenn der Leiter klein gegenüber der Isolationsdicke ist. Um die Rundheit zu kontrollieren wird kurz nach dem Spritzkopf mit Röntgenstrahlen die Schichtdicken in mehreren Achsen im warmen Zustand gemessen und es werden Proben am Ende des Produktionsprozesses vom Anfang und vom Ende des Kabels entnommen. Hier zeigen sich auch die Unterschiede in den beiden Produktionsarten. In Kettenlinien „hängt“ die Isolierung am Leiter und möchte nach unten fließen. Vernetzungs- und Kühlrohre können aber länger sein, als bei Turmanlagen. In Türmen fließt die Isolation gleichmäßig nach unten und die Kabel sind daher runder. Die Vernetzungs- und Kühlrohre sind aber in ihrer Länge durch die Turmhöhe begrenzt und bei konstanter Vernetzungszeit, ist die Anlage entsprechend langsamer zu fahren.
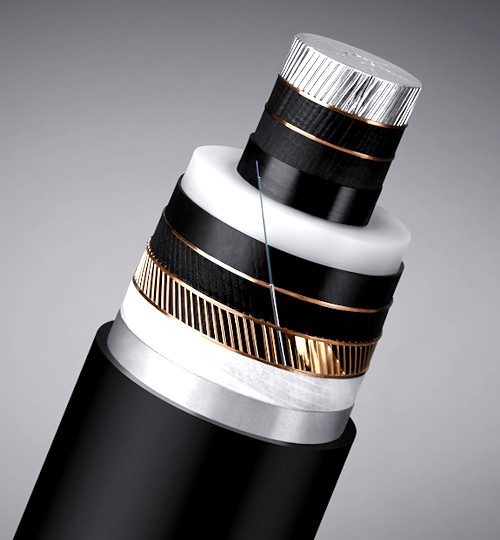
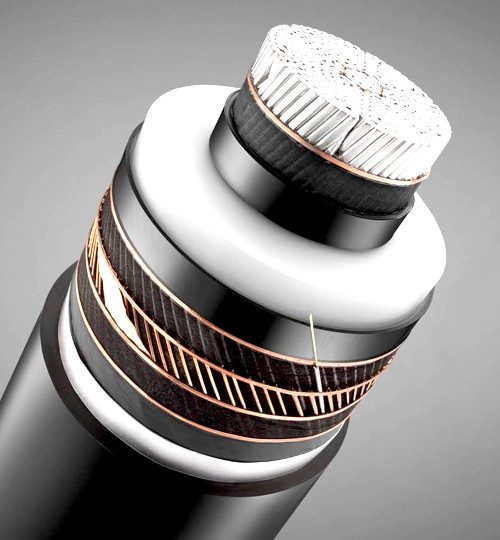
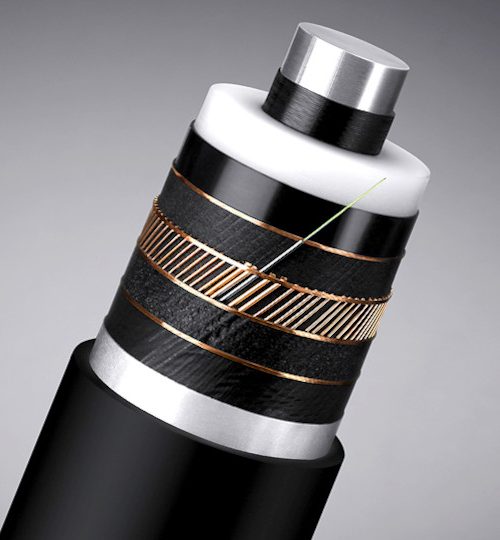
Erdung & PE Mantel
Schrim und Mantel HOchspannungskabel
Die Ader wir zunächst mit einem oder mehreren leitfähigen Bettungsbändern mit Quellmaterial umwickelt. Das soll die äußere Leitschicht vor Beschädigungen schützen, eine elektrische Verbindung von Schirm und äußerer Leitschicht herstellen und es ermöglich, dass sich der Schirm bei Biegungen zwischen Leitschicht und metallischer Umhüllung bewegen kann. Die Norm unterscheidet jetzt zwischen einem separierten und kombinierten Design. Bei einem separierten Design ist gemeint, dass jetzt das Kabel, optional mit einen oder mehreren Lichtwellenleiter im Stahlröhrchen, mit einem Kupfer- oder Aluminiumschirm aus mehreren einzelnen Drähten und einer Querleitwendel umwickelt wird. Der Schirm ist so auszulegen, dass im Kurzschlussfall der Kurzschlussstrom bei einer gegebenen Zeit getragen werden kann. In den nächsten Arbeitsschritten werden dann zunächst wieder eine oder mehrere Quellbänder umwickelt, um dann letztendlich „separat“ eine copolymere 0,2mm dicke Aluminiumfolie zu umlegen, auf die dann ein PE Mantel extrudiert wird und mit der copolymeren Schicht eine gut haftende Verdingung eingeht. Meistens kommt in diesem Prozess noch ein kleiner zweiter Extruder zum Einsatz, um eine sehr dünne leitfähige Schicht auf den Mantel zu extrudieren, um damit einen Manteltest auf der Kabeltrommel, im Rohr oder sehr trockenem Erdboden zu ermöglichen.
SAS Smooth Aluminium Sheath
Im Gegensatz dazu übernimmt z.B. ein SAS Mantel, ein sogenannter Smooth Aluminium Sheath, in einem kombinierten Design beide Funktionen. D.h. das Aluminiumrohr schützt radial vor Wasser und trägt im Fehlerfall den Kurzschlussstrom. Das hört sich zunächst kostengünstiger an, aber die Produktion ist technisch aufwendig. Zunächst wird mit einem Formwerkzeug ein Aluminiumband, um die Ader geformt und dann die Stoßstelle mit einem Laser geschweißt. In einem Tandemprozess wird dann das Aluminiumrohr durch Drucksteine reduziert, bis es sich auf die leitfähige Bandierung der Ader gelegt hat. Zusätzlich befinden sich in der Bandierung Kupfer oder Aluminium Bänder, um eine gute elektrische Verbindung zwischen dem SAS Mantel und der äußeren Leitschicht der Ader zu bekommen. Desto dünner das Aluminiumrohr gemäß Kurzschlussstromberechnung sein darf, umso schwieriger ist es den Umfang des Rohrs durch Schub auf Drucksteine zu reduzieren. Noch schwieriger wird es dann Lichtwellenleiter unter dem SAS Mantel zu integrieren, aber auch das haben einige Hersteller schon erfolgreich durchgeführt. Wie beim separaten Design wird danach ein PE-Mantel auf den SAS-Mantel extrudiert, allerdings muss vorher ein Klebemittel auf das glatte Aluminiumrohr aufgebracht werden, damit der PE Mantel gut auf der Aluminium Oberfläche haftet.
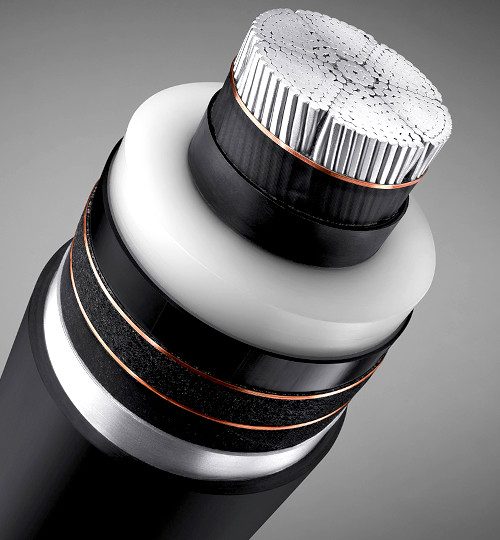
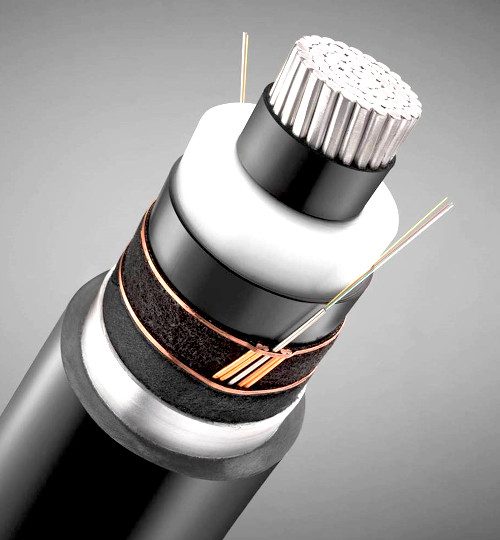

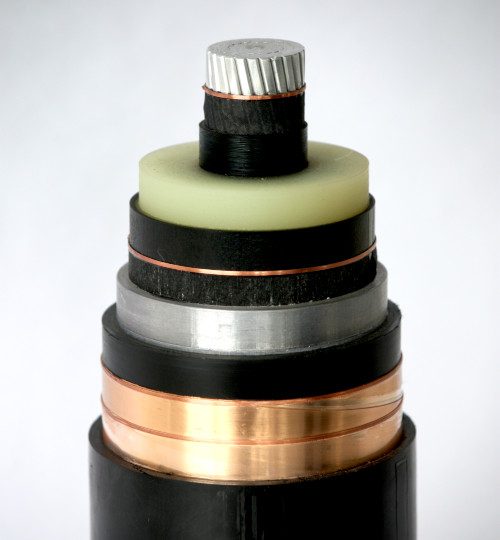
Quelle: Kabelbilder mit grauem Hintergrund Nexans
110kV bis 500kV
PRüfungen Hochspannungskabel & Systeme
Für Hochspannungskabel gibt es Prüfnormen – z.B. die IEC 60840 für Kabelanlagen bis 150(170)kV und die IEC 62067 für Kabelsysteme bis 500(550)kV. Zu berücksichtigen sind allerdings auch eine Vielzahl nationaler Normen, internationaler Normen oder auch Kundensonderspezifikationen, die sich meistens an die IEC anlehnen, aber im Detail unterschiedlich sein können.
Werksprüfungen - Routine Tests
Nach der Fertigung wird jedes Kabel elektrisch geprüft. Je nach Norm oder auch Werksvorschrift wird ein Vielfaches der Spannung an das Kabel angelegt, um das Kabel einer sehr hohen elektrischen Feldstärke auszusetzen. Hierzu werden in einem Hochspannungslabor in der Regel wiederverwendbare Wasserendverschlüsse eingesetzt. Das Wasser ist entionisiert und kann während der Prüfung gekühlt werden. Weiterhin wird ein Teilentladungstest durchgeführt. Auch hier ist es Normabhängig, wie hoch die Spannung und wie hoch die zulässigen Teilentladungen sein dürfen. Gute Hochspannungslabore haben einen geringen Grundstörpegel unter 1pC und erfahrene Messtechniker wissen, wenn Teilentladungen aus dem Kabel kommen, auch wenn der Grenzwert noch nicht erreicht ist.
Danach werden noch weitere elektrische Tests durchgeführt, wie z.B. ein Manteltest, wenn eine Leitschicht vorhanden ist und der Querschnitt des Leiters wird mit einer Gleichstromwiderstandsmessung gemäß „IEC 60228 – Leiter für isolierte Kabel kontrolliert. Dieser Test gehört zwar schon zur Stückprüfung, wird aber bei Abnahmen meistens zusammen mit den Routine Test im Hochspannungslabor durchgeführt. Wenn vorhanden werden noch die Dämpfungen der Multi- und/oder Singlemodefasern geprüft.
Stückprüfungen - Sample Tests
Zusätzlich werden an bis zu 10% der Längen, nicht elektrische Stückprüfungen gemäß vereinbarter Norm durchgeführt. Es werden Schichtdicken und Exzentrizität der Isolierungssystems und des Mantels gemessen, die Härte des Mantels und der Querschnitt des Schirms ermittelt. Auch das durchgängige Vorhandensein der Bänder und die vereinbarte Markierung des Mantels werden überprüft.
Wie bei Hochspannungskabeln üblich, kann noch ein Wassereindringungstest und ggf. ein Impulstest bei höheren Feldstärken Bestandteil der Stückprüfung sein.
Inbetriebnahme Prüfungen nach Installation
Nach der Verlegung und Installation des Kabelsystems wird jede Phase noch einmal geprüft. Um die Unversehrtheit des Mantels bei der Verlegung zu testen, wird wie in der Produktion ein Manteltest durchgeführt. Sollte es nicht möglich sein die Spannung am Schirm hochzufahren, kommt es durch eine Beschädigung am Mantel zu einem Durchschlag gegen Erde. Nicht ungewöhnlich ist es aber auch, dass die leitfähige Schicht in der Muffe nicht vom Mantel entfernt wurde.
Danach wird ein Spannungstest durchgeführt. Entweder mit einer Resonanzanlage mit 20 – 300Hz und einer erhöhten Spannung nach Norm oder Vereinbarung, oder es wird 24h die Betriebsspannung ohne Last angelegt. Zweifelsfrei ist der Test mit Resonanzanlage aussagekräftiger und es wird meistens sogar eine Teilentladungsmessung durchgeführt, die aber durch Störeinflüsse von außen, z.B. Regentropfen auf den Isolationsschirmen der Freiluftendverschlüsse, nur sehr erfahrene Messtechniker richtig deuten können.
Type & Präqualifikationstests
Je nach Norm und Feldstärke können sehr aufwendige Präqualifikationstests an einem neuen Kabelsystem, d.h. Kabel mit installierten Muffen und Endverschlüssen, nötig sein. Die einfachste Form sind Type Test nach IEC 60840. In einer vorgegebenen Testreihenfolge, der Start ist eine Biegeprüfung und tan d Messung, werden zwanzig Heizzyklen a 8 Stunden, mit mindestens 2h 95 – 100°C Leitertemperatur, gefolgt von 16h Kühlung, durchgeführt. Danach folgt eine weitere Teilentladungsmessung. Den Abschluss bildet dann ein Impulstest, der eigentliche Härtetest des Kabelsystems nach der thermischen Beanspruchung, ebenfalls gefolgt von einer Teilentladungsmesssung.
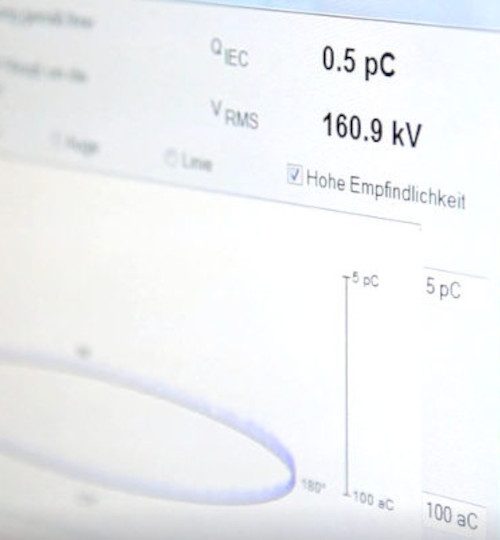
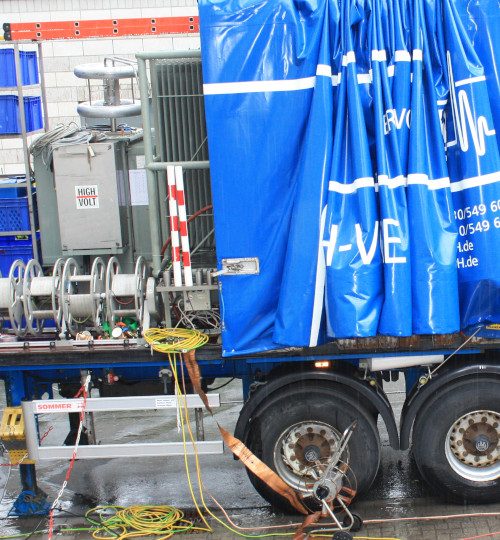
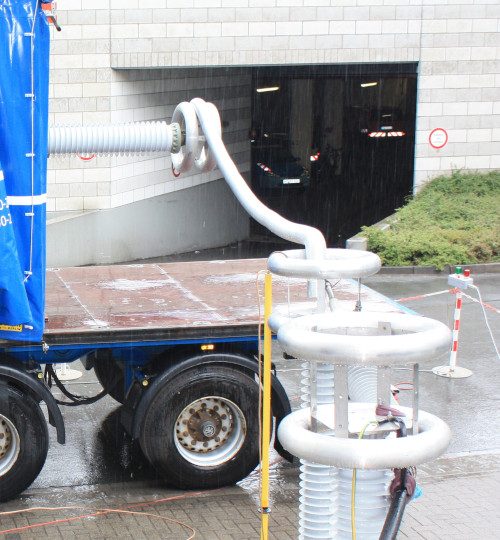